Cutting polyurethane foam is a major chunk of the entire PU foam industry. While we pay a lot of attention to the first building block of foaming, we also shouldn’t neglect the second step of conversion. This article will run you through the different types of industrial cutting when it comes to PU foam. And hey, got any further questions? Let us know.
Fundamentally, there are only two ways of cutting polyurethane foam: in straight lines and in irregular lines. Industry professionals further break down each type of cuts:
Cutting Straight Lines
We divide straight cuts into three categories:
- Vertical Cutting
- Horizontal Cutting
- Trimming
Vertical cutting refers to when the knife is vertical. This typically happens on two scales—on a larger scale for slabstock and on a smaller scale for trimmed blocks ready for conversion into consumer products. Vertical cutting machines for slabstock are also called block cutters. Block cutters come in two types, one with the blade going from floor-to-ceiling making transverse cuts across the foam, and another like a guillotine with the blade parallel to the ground.
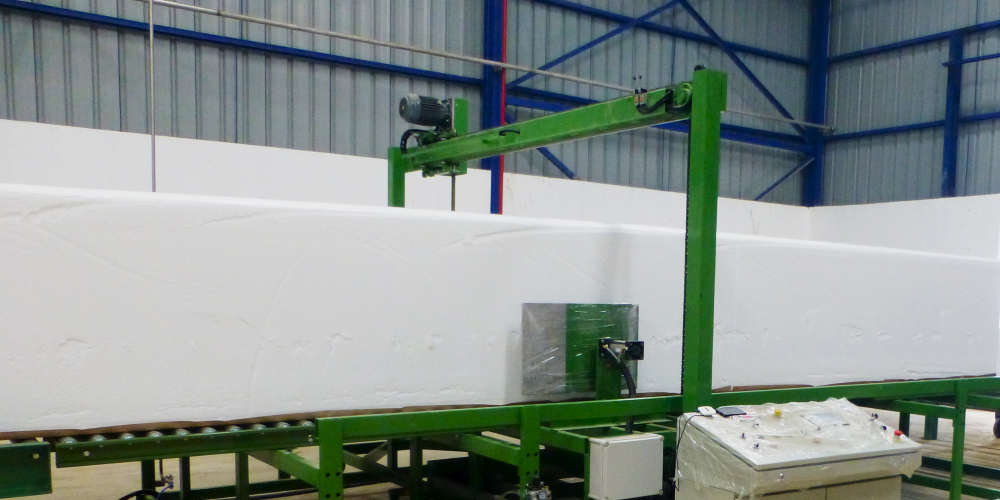
On a smaller scale, vertical cutting machines can also become angle-cutting machines; you can angle the blade from the overhead knife seat, enabling angular cuts for triangles, trapezoids, etc.
Horizontal cutting refers to when the knife is horizontal, and typically slices blocks of foam into thinner sheets. This can cut “sheets” as thick as latex mattress toppers or fabric-like sheets of foam used for apparel or quilting.
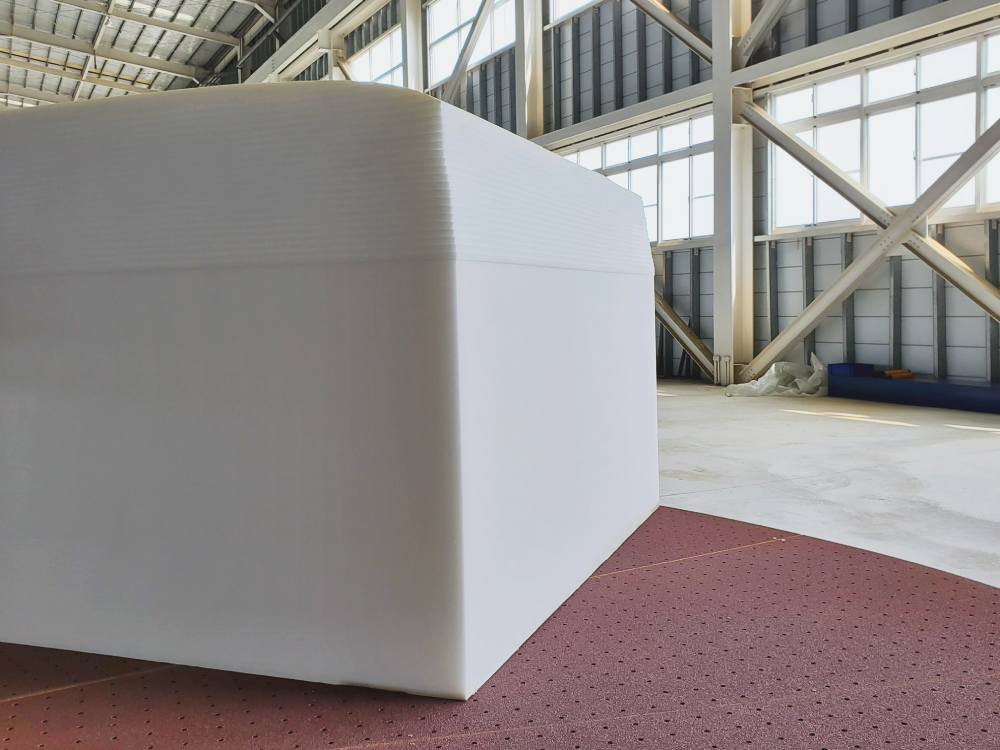
Trimming, then, can be a combination of vertical and horizontal cutting. New foam blocks have a natural skin on five sides that is typically trimmed away during conversion. Just one vertical cutting machine can suffice for trimming, of course, but plants with larger production quantities invest in machines specifically designed to trim all five sides without involving manual labor.
Cutting Irregular Lines
Straight lines are simple, but what if your product has irregular lines like curves or even spheres? These are ways to cut irregular lines:
- Manual cutting
- CNC cutting
- Compression cutting
- Milling
Manual cutting is self-explanatory. Patterns are put down on the cutting table or on the foam, and plant workers trace the patterns with the cutting machine by hand. The lack of digitization means cheap machines, but the trade-off is slower production and a higher margin of human error. (This is also the method of choice for DIY enthusiasts working with PU.)
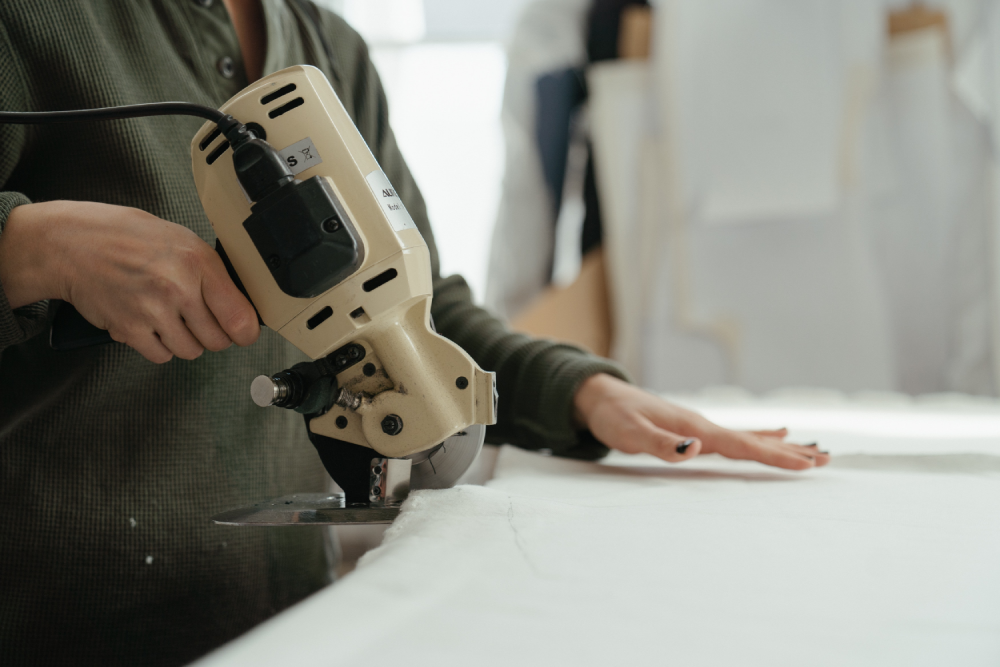
On the flip side, we have CNC, or computer numerical control cutting. You input cut patterns into the computer and the cutting process is completely digital. CNC guarantees consistent cuts each time and lowers labor costs. As an investment in automation, a CNC cutting machine is definitely worth its cost.
Another option for cutting out irregular shapes is compression cutting. Basically, a hydraulic mold stamps shapes out of a sheet of foam. This is the cutting method of choice for producing irregularly shaped sponges. Convoluting is another type of compression cutting by which foam sheets can be profiled—egg crate foam for padding and/or soundproofing are produced by this method.
Last but certainly not least, you can mill foam. If, for instance, you want to produce foam balls. All other cutting methods only work on at most 2.5 dimensions; they always leave one side flat. To produce completely round foam, you need a milling machine, which basically grinds away the foam using premade molds.
Takeaway
So, how to cut polyurethane foam? We count seven methods: vertical cutting, horizontal cutting, side trimming, manual cutting, CNC cutting, compression cutting, and foam milling. The topic of cutting polyurethane foam is not quite so simple, however. Foams at different hardness levels need to be cut at different speeds, different kinds of blades have different benefits—so on and so forth. Subscribe to our mailing list at the bottom of the page now to stay updated on the conversation.
Want to keep up to date on our company news? Take 1 minute to fill out the form below.